Development of a customized MES concept
A Manufacturing Execution System (MES) supports manufacturing companies to increase planning accuracy, process and product quality, equipment uptime and overall process transparency. Furthermore, acting as the central hub for manufacturing data, the MES is the basis for the Smart Factory. The automotive industry, in particular, has relied on IT-supported production control and supervision for years. This trend is increasingly followed by other industries as this case study of an agricultural machinery manufacturer shows. As part of a master-planning project, the company has asked Dürr Consulting to develop a MES concept tailored to the specific customer’s situation and vision.
Project challenges & approach
The customer has formulated the vision to develop a new production concept, which allows the efficient and flexible production of high-quality products. Due to reoccurring quality issues and a lack of comprehensive product tracking and documentation, the management has asked for a MES concept to control and supervise the new production system. However, the concept of a MES was new to the customer, as they hitherto had no such system in place. Hence, there arose the challenge of dealing with little existing MES knowledge and experience on the customer’s part during the concept development. Similar to the development of the layout and the concept planning for individual shops (e.g. paint), the MES concept planning followed a three-phase approach, comprising a status quo assessment phase, a concept planning phase and a detail planning phase.
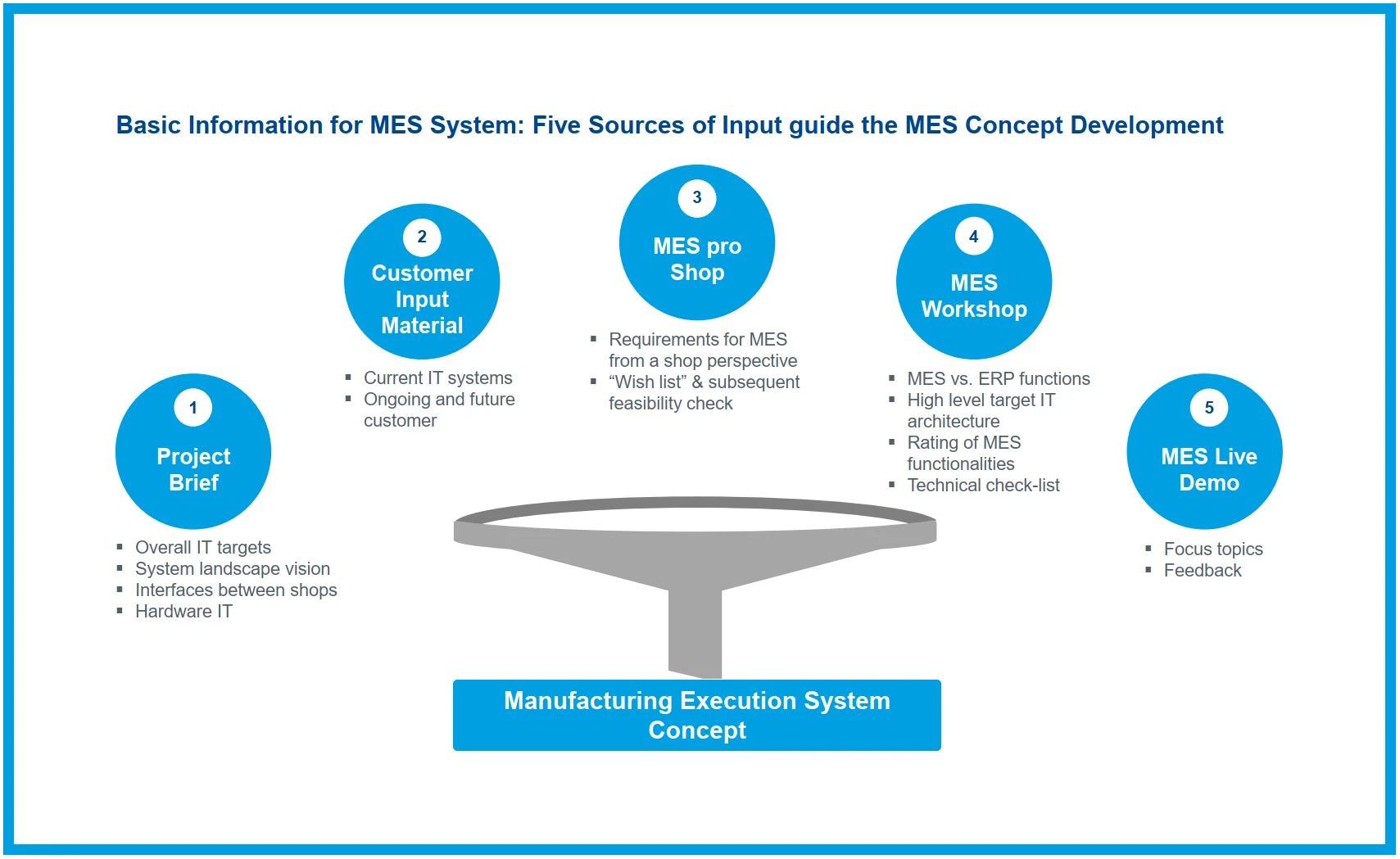
Status quo assessment
Targets of the customer regarding the IT systems have been agreed on as a basis for the concept development. To ensure that the new MES concept fits into the legacy IT infrastructure, the project team has reviewed documents of the existing IT landscape. As the IT infrastructure is usually subject to continuous adaptions, the planned introduction of IT systems has also been discussed. Thereby, it became apparent, that the customer already had several ERP add-ons in place, which cover to some degree the functionality of an MES system.
The image above provides an overview of the five sources of information that were considered as the basis for the subsequent development of the MES concept in the Concept planning phase.
Concept planning – from a general MES to a customer-specific MES concept
To enhance the customer’s understanding of MES systems and establish a common ground for further discussions, standard and vendor-independent MES functionalities, based on the renowned VDI norm 5600, were presented and discussed with the customer.
Based on the overview of MES functionality and the customer’s input, a joint MES workshop was organized. As some functions (e.g. order management) can either be realized in the ERP or in the MES system, the first objective of the workshop was to clarify whether the ERP or MES system is better suited for a specific function. The second objective was to evaluate standard MES functions in terms of their relevance for the customer – either mandatory, desired or optional.
After having established the big picture, including the current IT landscape as well as the customer’s requirements regarding factory-wide MES functionalities, the Dürr team proceeded to a more detailed discussion. Following the slogan MES pro shop, the team members in charge of planning a new concept for the paint, logistics, welding, assembly and testing shops reviewed the planned process to identify opportunities for process improvements due to MES system support. The resulting wish list was then evaluated by internal MES experts to determine whether the formulated use cases were feasible. Based on the shop planners’ input, a one pager was created per shop, describing the relevant use cases (e.g. worker guidance), along with the required hardware (e.g. fixed and mobile MES clients and bar code scanners) and the information flow (e.g. (1) from bar code scanner to MES, (2) from MES back-end to MES client and (3) from MES client back to the MES back-end). Finally, all MES use cases planned in the different shops were consolidated and explained in detail in a presentation.
To make the somewhat abstract MES functionalities more tangible and convey the look & feel of a state-of-the art MES system to the customer, MES live demos were conducted. The demo was organized as a combination of the presentation of prepared use cases and ad-hoc demonstrations of customer requests. The live demo proved to be effective in supporting detailed discussions about particular, customer specific requirements. In addition, it allowed an initial assessment of whether the customer’s requirements can already be met by a standard MES solution or whether custom developments are necessary. If different solutions were presented for a use case (e.g. shop floor material replenishment), customer feedback was noted and considered as further input for the customer specific MES concept.
Finally – taking all input into consideration (see Figure 1) – three MES concepts were developed and presented (see Figure 2). Each concept was designed according to distinct guiding principles. Concept 1 titled “Basic MES” followed a minimalistic approach, focusing on integrating only essential functions to keep CAPEX and OPEX at a minimum. The guiding principle of Concept 2 “Advanced MES” was to fulfill all of the customer’s mandatory requirements and the request for widespread application of worker guidance clients in the new factory. Concept 3 was guided by the maxim of exploiting the full potential of state-of-the-art MES systems and, in contrast to Concept 2, also included additional functions such as AGV control, manufacturing analytics and energy monitoring. Furthermore, it suggests the widespread use of mobile worker guidance systems in addition to the stationary ones. The three concepts are consolidated in a one pager (as indicated in Figure 2), stating the design principles of the concept as well as a concept’s advantages and disadvantages. Furthermore, a recommendation for one concept is given by Dürr along with the reasoning for the recommendation. To support the customer in the selection, a budget indication is given for each of the three concepts. The indication includes the CAPEX for software licenses, service costs for implementation and hardware costs as well as OPEX for maintenance and support. At the customer’s request, the proposed concepts can be updated, e.g. by adding a function to Concept 2 that was initially only available in Concept 3.
Your benefits at a glance
- The approach presented ensures several customer benefits
- Overview and introduction of modern MES system functionalities
- Vendor-independent consulting based on established industry standards & norms
- Look and feel of MES systems due to live demonstration
- Three concepts with a distinct guiding principle and pros & cons
- Well-founded recommendation
- Timeline and budget indication
- RFQ document tailored to the customer
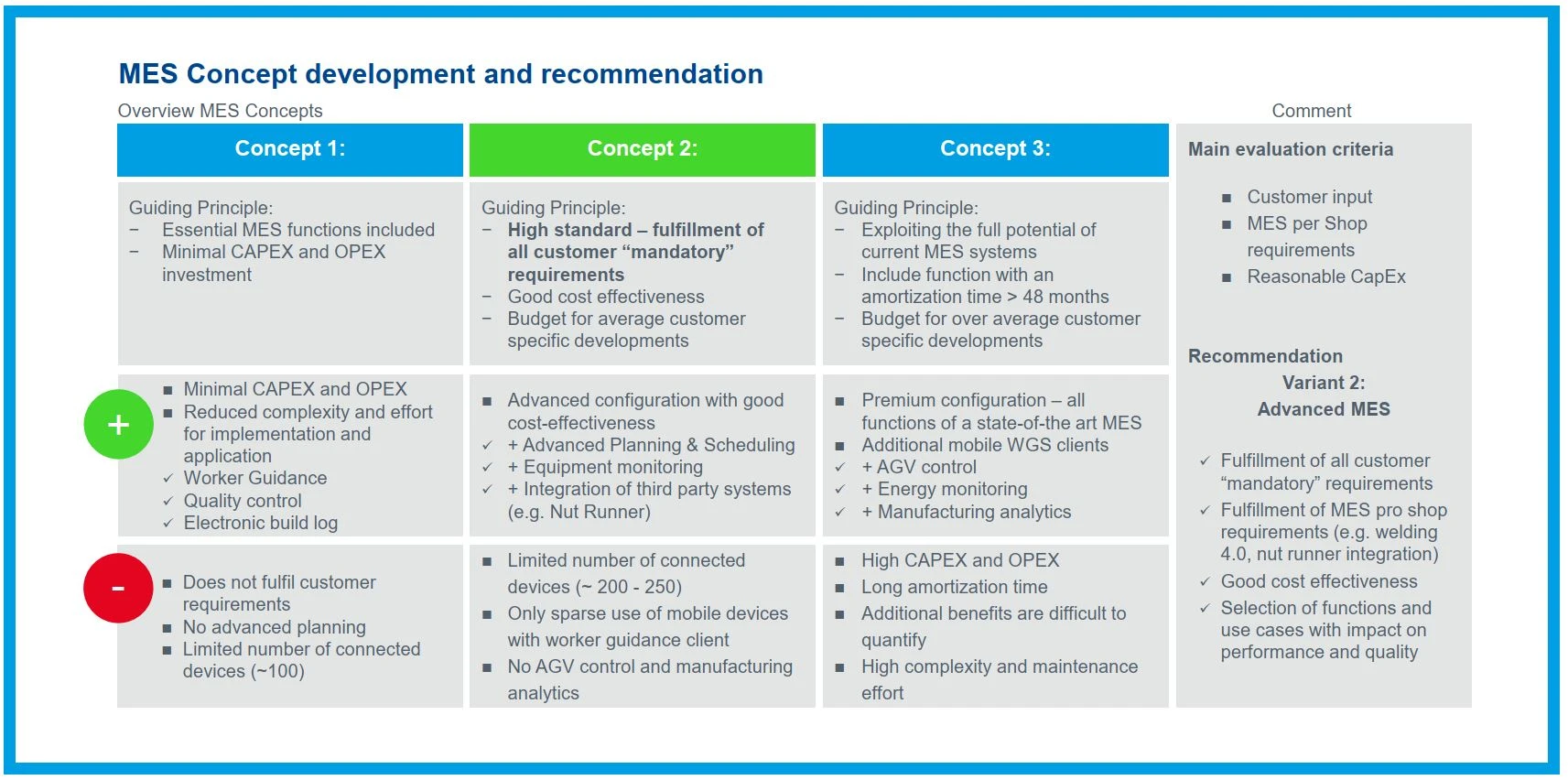
Detail planning
Once the customer has decided on a concept, the Detail Planning phase starts. In this phase, the concept is further detailed. In close collaboration with internal MES experts and based on already realized MES projects, a project timeline comprising the essential implementation phases is prepared. The timeline allows customers to select a suitable date to request quotes of MES vendors that allows the selection and implementation of the new system so that it is ready by the planned SOP. Based on the current planning status of the individual shops and the planned MES use cases pro shop, a list of necessary hardware is compiled. Usually, this list includes the following hardware components: server, desktop computers, fixed installed and mobile MES clients, Andon boards, scanners and printers. By consolidating all hardware requirements of the MES system across all shops, a detailed equipment and budget list is provided to the customer in addition to the concept.
Request for quotation documents
The final step in the detail phase is the creation of the request for quotation (RFQ) document. The jointly approved MES concept is the basis for the RFQ document, thus ensuring that vendors can propose suitable solutions to the customer specific context and requirements. The RFQ document for MES systems comprises three main chapters. The first chapter, scope of delivery, describes the scope of the requested service and software and provides some context information about the customer’s situation, objectives and expectations. The second chapter, functional requirements, comprises, on the one hand, general, factory-wide applicable functional requirements such as alarm, track & trace and KPI & trends and on the other hand, shop-specific requirements such as process parameter monitoring in the paint shop. The third chapter describes all non-functional requirements. These include technical requirements, such as availability and accuracy as well as non-technical requirements such as customizing, training, documentation, maintenance and support.